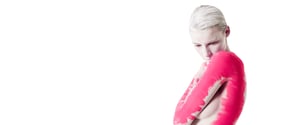
Assessment of absorbency of mopheads
By Hugo Corstjens
Introduction
Whenever spills or contamination occurs in a cleanroom environment, staff must have access to appropriate cleaning tools. Mops fulfil an indispensable role in the management of contamination in controlled environments. The material from which a mophead is made and the way it is manufactured determine its characteristics concerning cleanliness (particles, ions, non-volatile residue, linting), strength (tensile strength, bursting strength, abrasion resistance), and functional characteristics (absorbency). An accurate comparison and the final selection of the mophead will to a significant extent determine whether the stringent conditions in the cleanroom will be met1. In this paper, we will look more closely at the various aspects of mophead’s absorbency. Only when there is sufficient insight into this parameter, a proper comparison and selection can be made.
Absorbency parameters and their meaning
Absorbency is used to describe the ability of a fabric to take in moisture and, by extension, the ability to pick up particulate matter. The Institute of Environmental Sciences and Technology (IEST) has published a recommended practice (IEST-RP-CC004.3) describing methods for evaluating wiping materials used in cleanrooms and other controlled environments for characteristics related to both cleanliness and function, including absorbency2. Absorbency is expressed as the sorption characteristics and rate. Quantification of these parameters is typically deduced from a static test. Dynamic tests, which differ from static tests that they involve movement of the cleaning tool to simulate realistic conditions of use, also exist3. However, most specification sheets report values from static tests, so they seem more appropriate for comparison mops.
The efficiency of a mophead will depend on the fibre or base material and the construction details. Microfiber (or microdenier4, 5) materials are used in the fabrication of wipers and mopheads6, and appear to be superior in terms of liquid removal effectiveness. Because of the differences in composition and construction, their basis weight, which is the weight per unit area expressed in gram/square meters, can vary widely among mopheads. These values roughly range from 200 to about 800
. In the case of two materials with the same base weight but a different denier or D-value of the yarn, the material with the lower D-value will have a greater surface area per unit volume and consequently higher liquid absorbency values.6
This property is captured by the absorption efficiency, which is defined as the amount of liquid, mostly water, that can be absorbed by 1 gram of the material. This value roughly ranges from 2 to 7
. As an example, an absorption efficiency of 3
indicates that the material is capable of absorbing three times its weight in water. This value is very useful for comparing the intrinsic properties of different materials.
The materials are processed into a fabric by weaving, thermal bonding, melt-blowing, or knitting. The absorbency of such a fabric is represented by its absorption capacity, which is expressed in milliliter/square meters. According to the aforementioned IEST recommended practice, absorption capacity is determined by the difference in weight between a dry piece of material and the same material immersed in a tray of water for 60 seconds. The weight difference represents the weight or volume of water absorbed7. This value must be divided by the surface area of the sample material to obtain the absorption capacity and ranges roughly from 1500 to 8000
. This appears to be a more practical definition of the ability of a mop to absorb liquid.
Absorption capacity and efficiency are related via the equation:
Where abseff is the absorption efficiency in , abscap is the absorption capacity in
, and Wtbasis is the basis weight or the weight per unit area of the fabric in
.
The third parameter that relates to absorbency is the rate of absorption. This value represents the time it takes a mophead to absorb a liquid. Depending on the settings, the rate of absorbency may or may not be a critical parameter. It is however obvious that a (too) low rate of absorption is inconvenient and may ultimately lead to a reduction in cleaning efficiency, through a shift towards non-compliant materials or procedures.
Conclusion
The choice of mophead is critical as it can affect the final cleanliness obtained. In this paper, we discussed different metrics to describe absorbency. Absorption efficiency and absorption capacity allow to evaluate the absorption characteristics of the material and the fabric respectively. The rate of absorption should also be taken into account to avoid inconvenience and improper use of cleaning materials. The overall absorbency of a mophead is captured in these parameters and they must be used to select the mophead that meets all needs.
References
- Kalelkar, S., & Postlewaite, J. (2011). Consistency as the True Measure of Cleanroom Wiper Quality. Journal Of The IEST, 54(2), 75-84. https://doi.org/10.17764/jiet.54.2.j6367818507386l7
- IEST-RP-CC004.3. (2019) IEST-RP-CC004: Evaluating wiping materials used in cleanrooms and other controlled environments available at https://www.iest.org/Standards-RPs/Recommended-Practices/IEST-RP-CC004
- Oathout (2000). Determining the Dynamic Efficiency with which wiping Materials Remove Liquids from Surfaces. International Nonwovens Journal. https://doi.org/10.1177/1558925000OS-900113
- Denier is a unit of measure for the linear mass density of fibers, and is the mass in grams per 9000 meters of the fiber. Silk has a DPF (denier per filament) of roughly one. Microfiber has a DPF below 1 but is otherwise not very well defined.
- Clarke, G. (2019). Microfiber – a Defined Term that requires Explanation and Understanding [Blog]. Retrieved 6 April 2022, from https://aatcc.org/microfiber-defined/.
- Skoufis and Cooper. (2003). Microdenier fabrics for cleanroom wipers. In Mittal (Ed), Surface contamination and cleaning, Volume 1 (pp. 267-277). VSP
- It is assumed that the density of water is 1gml.