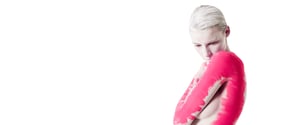
Choosing the perfect cleanroom wipe:
An In-Depth investigation
Abstract
In pharmaceutical environments, upholding stringent cleanliness standards is essential to safeguarding product integrity and ensuring consumer safety. Cleanroom wipes play a critical role in maintaining the integrity of controlled environments across various industries. This paper provides a thorough analysis of selecting the optimal cleanroom wipe specifically tailored to the requirements of pharmaceutical environments. Let’s delve into the key considerations for choosing the right cleanroom wipe, exploring the differences in fabric types, structures, edge configurations, and the diverse functions these wipes serve. By comprehending these factors, decisions tailored to meet the precise demands can easily be made. |
![]() |
Introduction
Cleanroom wipes are fundamental tools in environments where contamination control is important. The selection of the appropriate cleanroom wipe is key to ensure optimal cleaning, disinfection, and particle retention. This paper provides comprehensive guidance through the complexities of cleanroom wipes, emphasizing the importance of material composition, wipe structures, edge types, compatibility, and functional characteristics in both cleaning and disinfection processes(1). |
Material Types:
Cleanroom wipes are manufactured from a variety of materials, each with unique properties that influence their performance(2). These materials include both natural and synthetic fibers, each bringing unique benefits to the variety of cleanroom wipes available. |
Polyester (Synthetic):
Lyocell (Semi-synthetic):
Blended materials (Combination of Natural and Synthetic):
|
Microfiber (Synthetic):
Viscose (Semi-synthetic):
|
Wipe structures
Knitted Wipes: produced by interlocking loops of long fibers, knitted wipes offer stretchability and conformability. They are suitable for applications where wiping irregular surfaces is necessary and provide good absorbency. The 3D structure gives excellent absorption qualities and increased dirt absorption. |
Woven Wipes: constructed by weaving long fibers together, woven wipes are durable and have high tensile strength. They are not elastic and have a 2D structure. The tighter structure than knitted material results in a lower absorption. They are suitable for applications requiring abrasion resistance and repeated use. |
|
Non-Woven Wipes: most high-quality nonwovens are made with a spunlaced process which hydroentangles short fibers together using high-pressure jets of filtered water to clean the fabric during the manufacturing process. |
Edge configurations
Knife-Cut:
Laser-Cut:
|
|
Ultrasonic Sealed:
Sealed Border:
|
Choosing the right wipe:
Cleanroom Class: match the wipe's cleanliness level to the cleanroom classification. Material compatibility: ensure the wipe is compatible with the surfaces and chemicals in use. Pure synthetics such as polyester nonwovens and knitted fabrics offer the greatest range of chemical compatibility. Wipes containing natural fibers like cellulose are susceptible to degradation caustic solutions and are not suitable for use with all disinfectants |
Task requirements:
choose the appropriate fabric, edge, and size based on the task at hand. Environmental considerations:
Wipes made out of recycled 100% knitted polyester provide a sustainable solution for critical environments without jeopardizing quality or performance Budget considerations:
balance performance with cost-effectiveness |
Selecting the right cleanroom wipe is crucial for optimal cleaning, disinfection, and particle retention in controlled environments. This involves considering material types, wipe structures, edge configurations, and specific application needs. Material options range from synthetic (polyester, microfiber, polypropylene) to natural (cellulose) and semi-synthetic (viscose, lyocell), each with unique properties. Understanding wipe structures, such as knitted, woven, and non-woven, helps tailor the choice to performance requirements. Edge configurations, like knife-cut, laser-cut and ultrasonic sealed, play a significant role in particle release prevention and cleaning effectiveness. To make the right choice for a cleanroom wipe, factors such as cleanroom class, material compatibility, task requirements, environmental considerations, and budget must be carefully evaluated. Matching the wipe's cleanliness level according to the ISO 14644 classification to the cleanroom classification, considering material compatibility with surfaces and chemicals, and selecting the appropriate fabric, edge, and size based on the task are critical steps. Additionally, environmental sustainability and budget considerations should be balanced with performance needs. A comprehensive understanding of material properties, wipe structures, and edge configurations is essential for informed decision-making in the complex landscape of cleanroom wipes. |
Conclusion
References
(1) ISO 14644: Cleanrooms and Associated Controlled Environments(2) C.L. Ward, S.P. Richardson, K. Warwick, "Fundamentals of Cleanroom Wipe Selection"
(3) M.K. Alam, S. Kumar, "Cleanroom Technology: Fundamentals of Design, Testing and Operation"