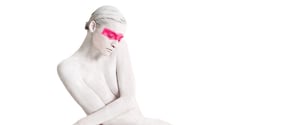
Cleanroom Goggles:
A guide to selection
By Gordon Farquharson
Introduction
This paper provides information about Cleanroom Goggles. It reviews the applicable regulatory requirements and technical standards, and suggests a routemap or checklist to help with a logical selection process. | ![]() |
Cleanroom Personal Protective Equipment (PPE) is unique in the world of PPE because it has two fundamentally different objectives. These are (a) safety protection of the wearer, and (b) protection of the process or product from contamination disseminated by the wearer. It is also essential that goggles are comfortable to wear. Comfort features include physical fit, optical performance and ventilation.
|
Roles and responsibilities:
Your goggle supplier should take responsibility for designing and supplying a product that meets the safety and contamination control objectives. |
Goggle procurement check-list
a) Supplier qualification:
Note: Some safety goggle are specified for protection against welding sparks and exposure to gases. Such hazards aren’t normally found in cleanrooms d) Goggles life-cycle/use
|
e) Durability
f) Comfort
g) GMP check-list
|
Conclusion
Ultimately, the success of the cleanroom goggle selection process relies on prioritizing safety, cleanliness, and compliance with established regulations and standards. By addressing these factors holistically, organizations can create an effective barrier against contamination while ensuring the safety and comfort of their personnel in the cleanroom environment.
References
(1) August 2023EudraLex: The Rules Governing Medicinal Products in the European Union, Volume 4 EU Guidelines to Good Manufacturing Practice Medicinal Products for Human and Veterinary Use
Annex 1: Manufacture of Sterile Medicinal Products (corrected version)
The requirement to use Cleanroom Goggles is being driven by the GMP Annex 1, which states that: ".... a sterile face mask and sterile eye coverings (e.g. goggles) should be worn to cover and enclose all facial skin and prevent the shedding of droplets and particles...."
(2) US FDA warning letter - goggles
2016. In 2016 a US Food and Drug Administration (US FDA) warning letter to a manufacturer of pharmaceuticals, warned that the cleaning and disinfection process for goggles used in aseptic cleanrooms could not guarantee sufficient protection to eliminate contamination. The regulatory authorities require fully documented validation studies resulting in effective and reproducible processes.
(3) Regulation (EU) 2016/425 on personal protective equipment
Regulation of the European Parliament and of the Council of 9 March 2016 on personal protective equipment and repealing Council Directive 89/686/EEC (with effect from 21 April 2018). Now covers the whole PPE supply chain.
(4) Regulation (EC) No 765/2008 of the European Parliament and of the Council of 9 July 2008 setting out the requirements for accreditation and market surveillance relating to the marketing of products and repealing Regulation (EEC) No 339/93.
(5) ANSI/ISEA Z87.1-2020 Standard (a US derived common standard)
Prescribes the design, performance specifications, and marking of safety eye and face products, including safety goggles, spectacles, faceshields, and welding helmets, worn by workers in thousands of manufacturing and processing facilities, university and research laboratories, and other occupational settings.
(6) Medical device specification of Moist heat sterilisation
ISO 11134:1994 Sterilization of health care products — Requirements for validation and routine control — Industrial moist heat sterilization.
(7) New cleanroom standard
ISO/WD 14644-18:2023 Cleanrooms and associated controlled environments — Part 18: Assessment of suitability of consumables.
Note: This standard is a check-list of matters to be considered. There are some supporting informative appendices providing additional guidance. It does NOT include any product technical specifications or requirements.
(8) EN 166:2001 Requirements for protective eyewear
EN 166:2001 is the European standard covering the requirements for protective eyewear. It is closely linked to EN 167:2001 and EN 168:2001 which specify the optical and non-optical test methods.
(9) ISO 9001:2008 Quality system for manufacturing.
(10) ISO 14001:2015 Environmental Management.